Intent on both making good products and keeping the environment clean
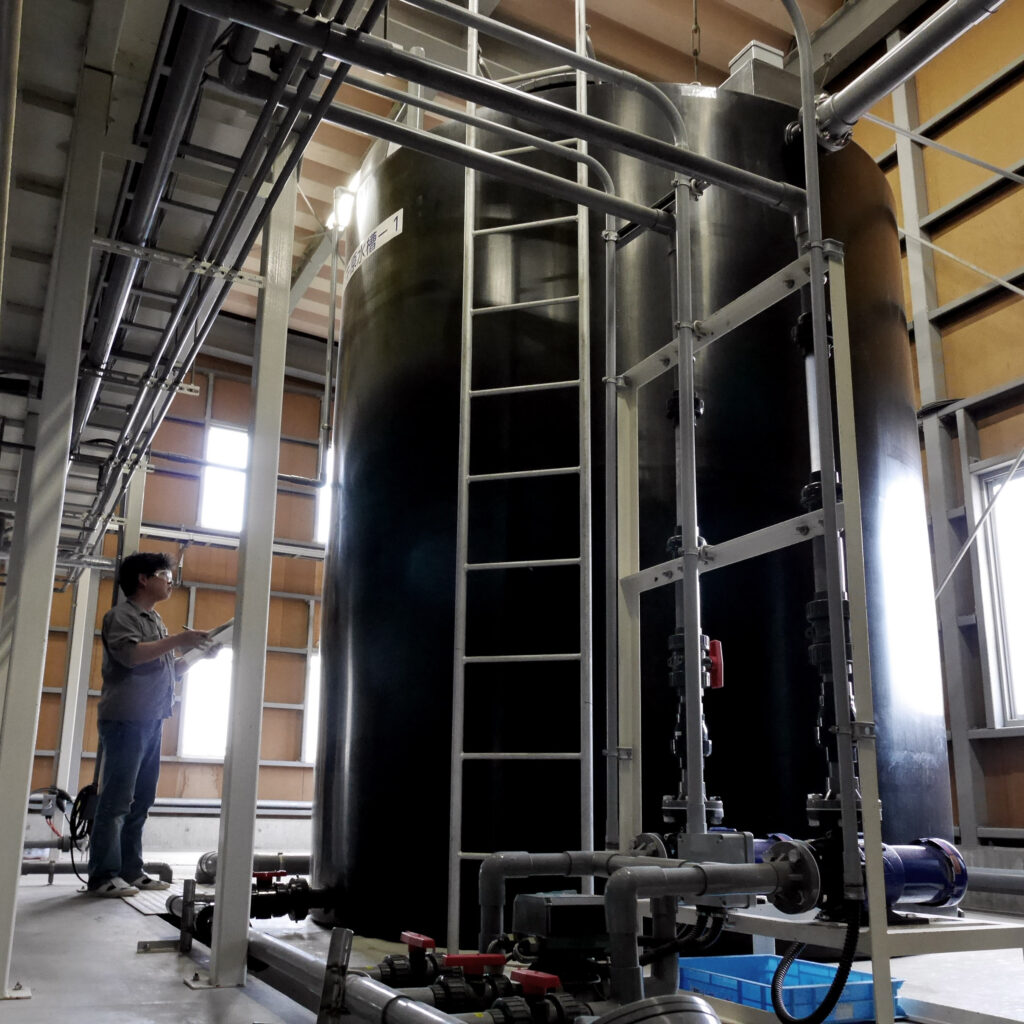
The exterior of a high-end interchangeable lens that the user is proud of owning and feels pleasure in operating should be made from metal rather than plastic. As a surface treatment, plating has been traditionally used. Many of you must have been excited about the texture of glittering chrome that accentuates a feeling of precision or plated nickel that creates a warmth and nostalgic look despite being a metal. In recent years, the number of unplated interchangeable lenses has increased. This is because many products do not have a metal exterior. Another reason is that manufacturers are trying to avoid the cost of treating wastewater discharged from the plating process. Realistically, the detoxification of plating wastewater requires large-scale facilities. The above photograph shows a storage tank of plating wastewater installed in the dedicated facility at Cosina’s Nakano factory.
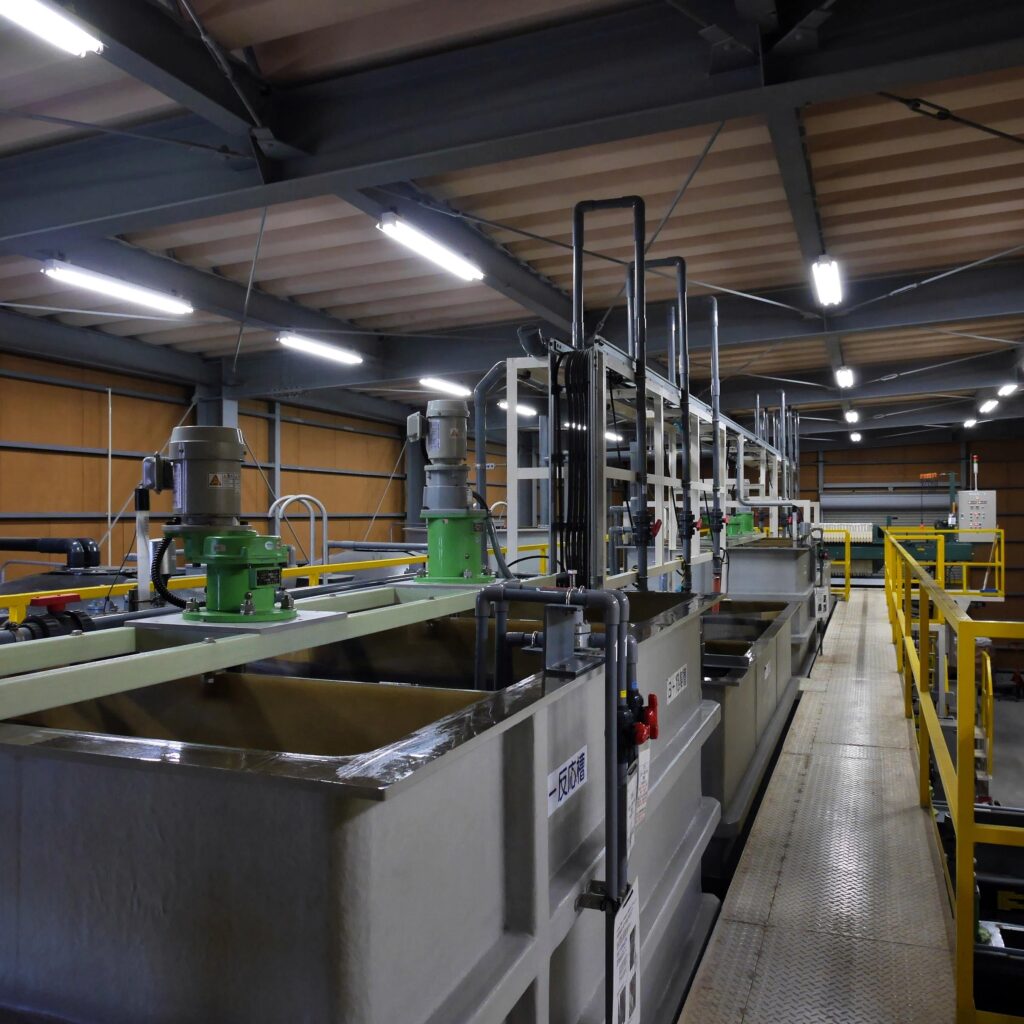
There is inevitably a washing process in plating. This process generates wastewater containing metals such as chrome and nickel. In 1950’s to 1970’s, pollution caused by the discharge of such wastewater into rivers gained prominent attention. Today, rigorous environmental quality standards are in place, so wastewater is cleaned by a chemical method called “coagulative separation” in which metal particles are detoxified, precipitated out and ultimately extracted by a filter press that has a large pressure of about 0.5 MPa. The removed metal components (sludge) are made into cakes by dehydration treatment and transported from the site for treatment as industrial waste. This process requires a 100% yield rate and, so that failures that could cause environmental pollution never occur, the operation continues with meticulous care. And, the treatment facilities are cleaned much more thoroughly than our manufacturing sites.
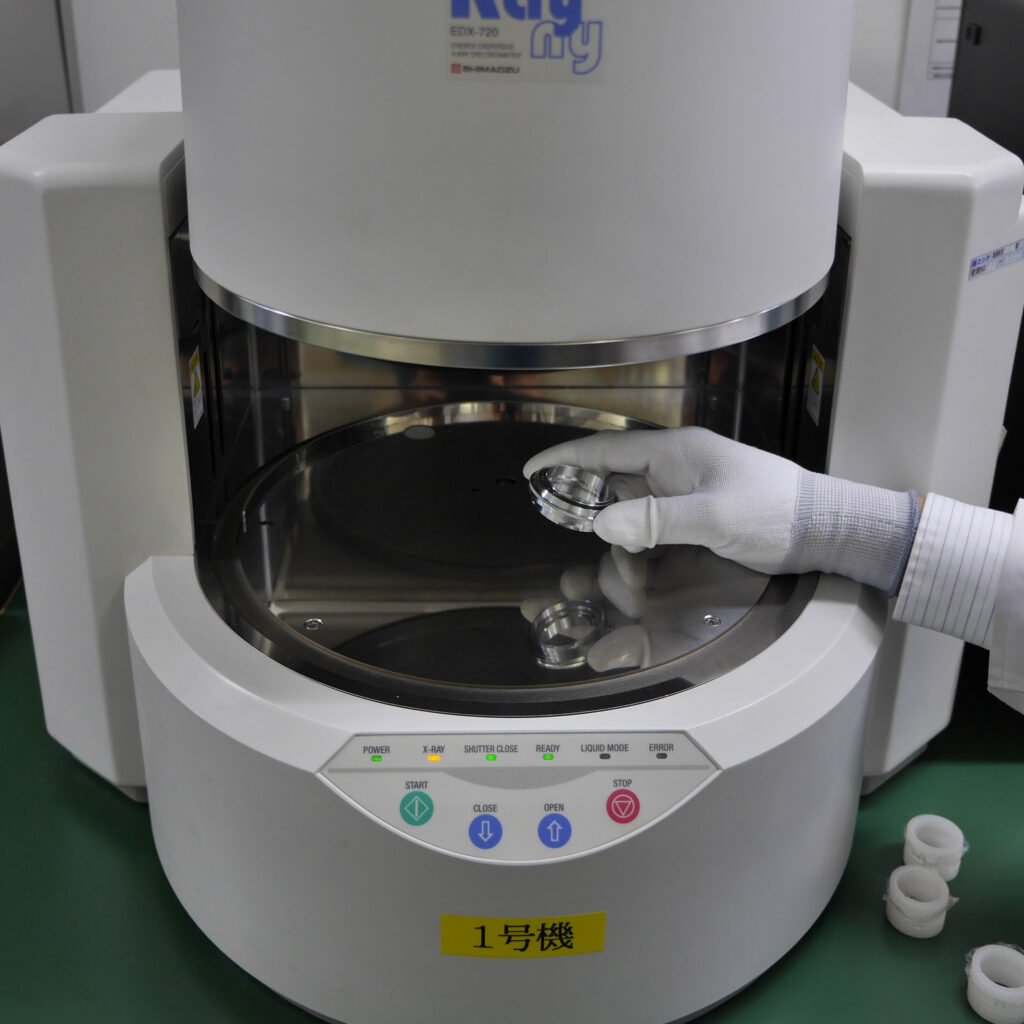
Also, with the aim of preventing even trace amounts of hazardous material in products delivered to users, we check the materials of high-end optical products manufactured by Cosina with an XRF inspection machine. All elements that constitute products, ranging from metal components and screws, and optical glass to coating, are subject to this inspection. This special equipment allows non-destructive measurement of elemental components and component rates. Only after confirming that specific toxic substances such as cadmium, lead, mercury, hexavalent chromium, and polybrominated biphenyl are not contained in the material at all, and when the safety of all materials is ensured, we start manufacturing. Cosina is continuing such rigorous efforts everyday not only with the wish of making products of good quality and appearance but also keeping the environment where we live clean.