Barrel polishing to a uniform size, weight, shape and grain

Prior to grinding, lens blanks are formed by press-molding. In that process, the most important thing that determines lens quality is the weight of the optical material and the surface finish. The above photograph shows a piece of manually cut glass (left) and a worked piece glass that was made to the necessary weight by barrel polishing (right). Lying below the two pieces of glass are polishing stones. In barrel polishing, optical glass, polishing stone, abrasive and water are mixed in set proportions and rubbed together in the barrel rotated at a constant speed. As optical glass after barrel polishing has round edges, pressure during press-molding is not uniformly applied to the glass, which prevents the glass components from cracking and crystallizing.
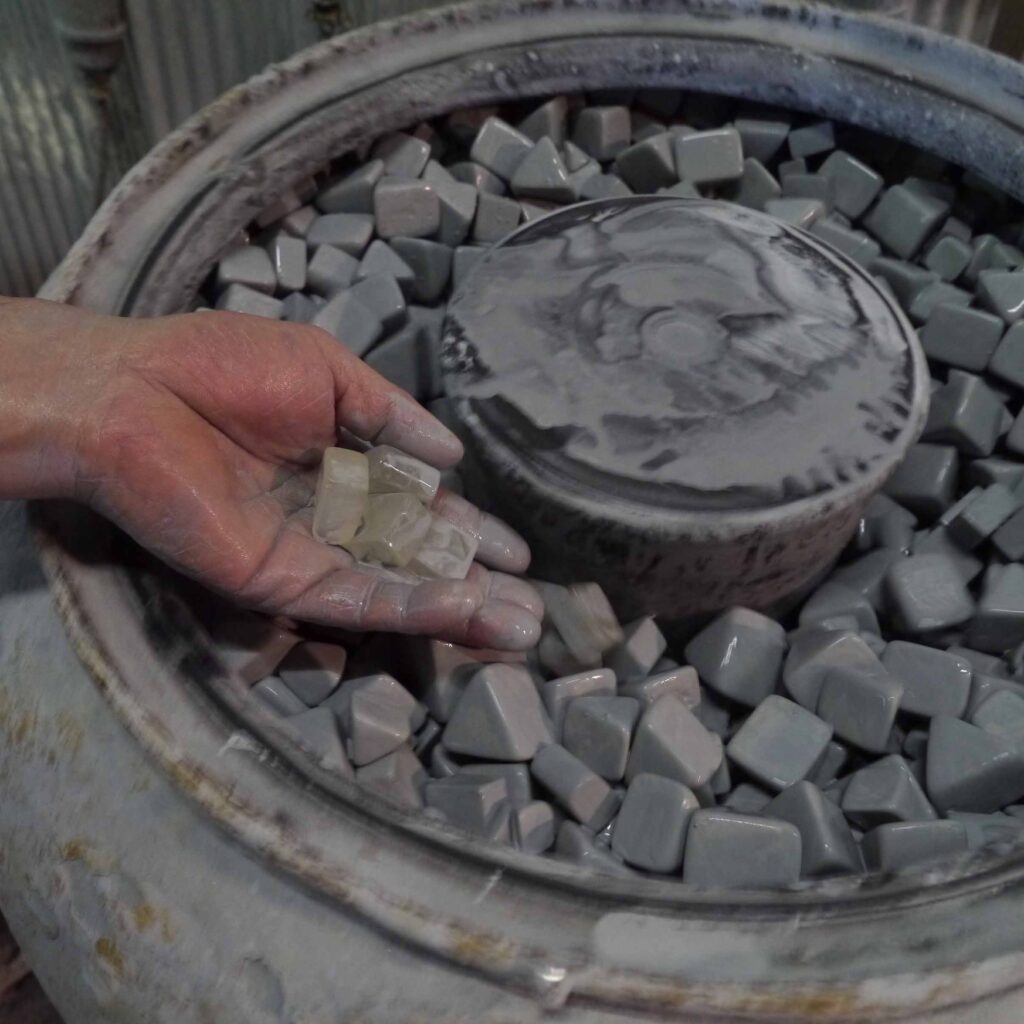
At Obuse factory, barrel polishing is done in any number of ways depending on the targeted finishing weight of the cut optical glass. Here, we explain the operations with a vibration barrel polishing machine. This machine uses three-dimensional vibrations to move the contents in the barrel tank and create frictional force. A batch of the heaviest cut optical glass as determined by on precise weighing is first added to the barrel. Then, pieces of cut optical glass are regularly taken out of the barrel and weighed. When the weight of the first batch reaches the same weight of the second heaviest batch, the second batch is added. The polishing and weighing procedure is repeated in the same way, to add the third batch. In the end, all the pieces of cut optical glass have the same weight, round edges and a uniform grain.
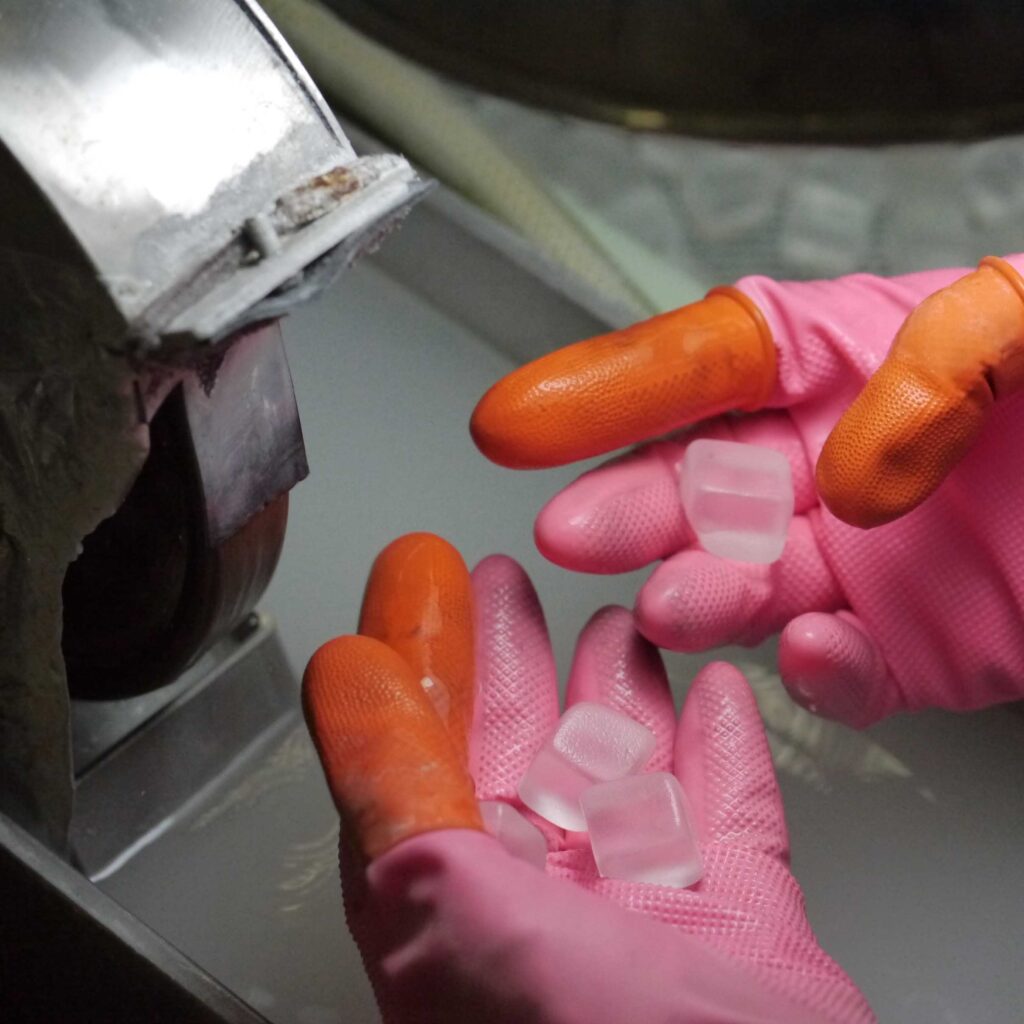
The polished pieces of optical glass are checked and any small scratches, are removed before being sent to the press-molding process. Individual pieces of glass are visually checked and, if even the slightest problem is detected, they are manually rubbed with water using diamond grindstones. The series of processes for cutting optical glass, barrel polishing the pieces to a uniform weight and removing scratches can only be done by hand. It is difficult to replace these operations with a machine, which leaves us with the choice of continuing or abolishing these practices. So, our opting to these processes by hand shows our affection for optical glass materials as the origin of high-end optical devices and our instinct desire to finish all materials into good products.