Selecting and preparing polishing pads

The above photograph shows a number of polishing plates used in lens polishing process. Cosina has a variety of these plates in different sizes and curvatures. They are used to finish optical elements that have been smoothed with diamond pellets (see 017) to the curvature radius and optical precision specified in designs. They furthermore serve to remove any minute scratches or rough spots from surface of optical elements. A variety of polishing pads are used to do this. These pads are selected according to the type of element to be polished and the grain and properties of the abrasive used in polishing.
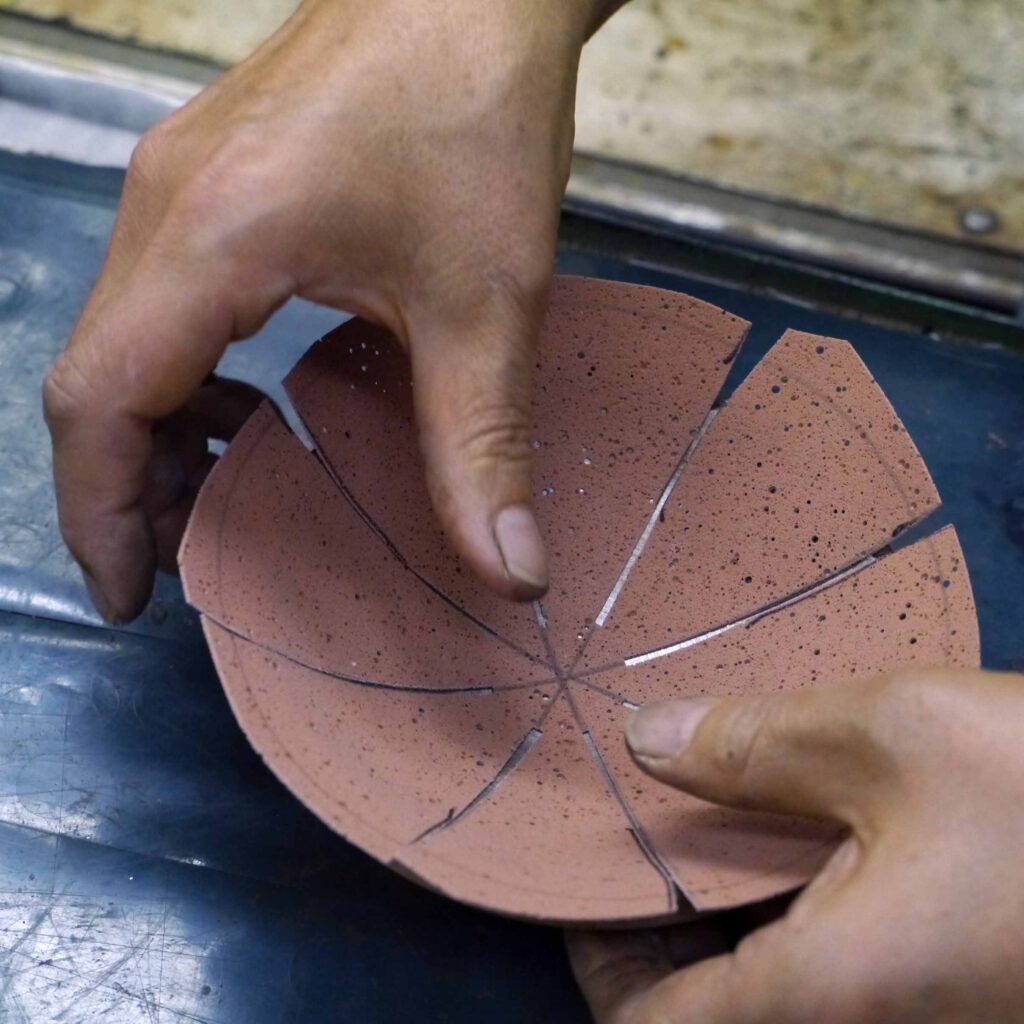
Whether concave or convex, a polishing plate is semispherical and, therefore, has a specific radius. On it a urethane or a suede-like polishing pad is attached by hand. With a convex plate, this job is similar to affixing a map of the world to a globe, only that the pieces attached to a globe are overlapped slightly while the leafs of a polishing pad must not overlap or bunch even the slightest. What is the key to ensuring high quality polishing is that the polishing pad has a single consistent thickness when attached on polishing plate. Also, to keep the pad from overlapping or bunching, narrow slits are made in the pad. This work is done carefully to make sure these slits are evenly spaced apart.
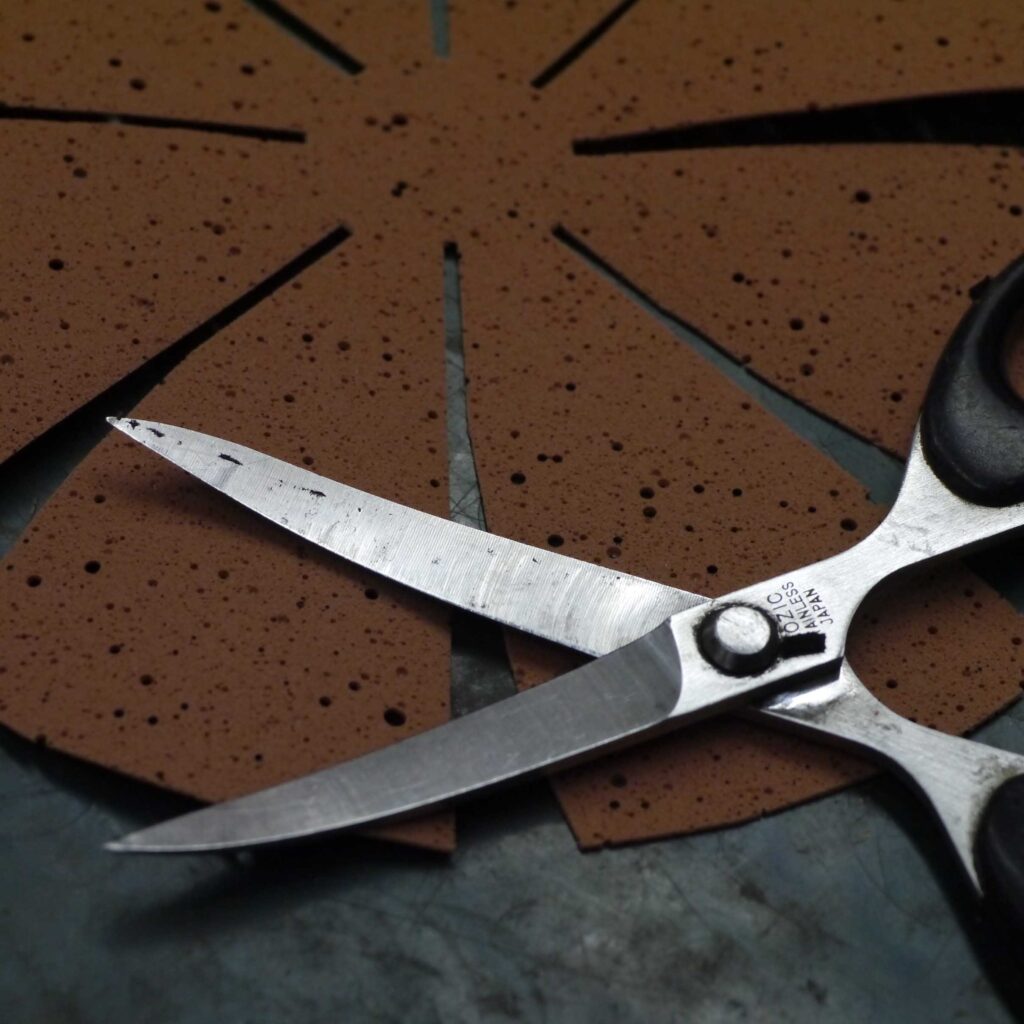
Polishing pads are cut in the shape of a flower petal. If looked at closely, the slits between adjacent leafs gradually widen from the center towards the edges so that the slits are the same width from top to bottom when the pad is attached to the polishing plate. Each pad is customized to the size and curvature of the polishing plate. Curved blade scissors are used because they are suited for cutting curves. Experienced skilled workers carefully cut out the pad and attach it to the polishing plate by hand. Because of these dexterous preparations, the optical elements are polished to a high degree of profile precision and visual beauty.