Plating to perfection by hand and eyesight
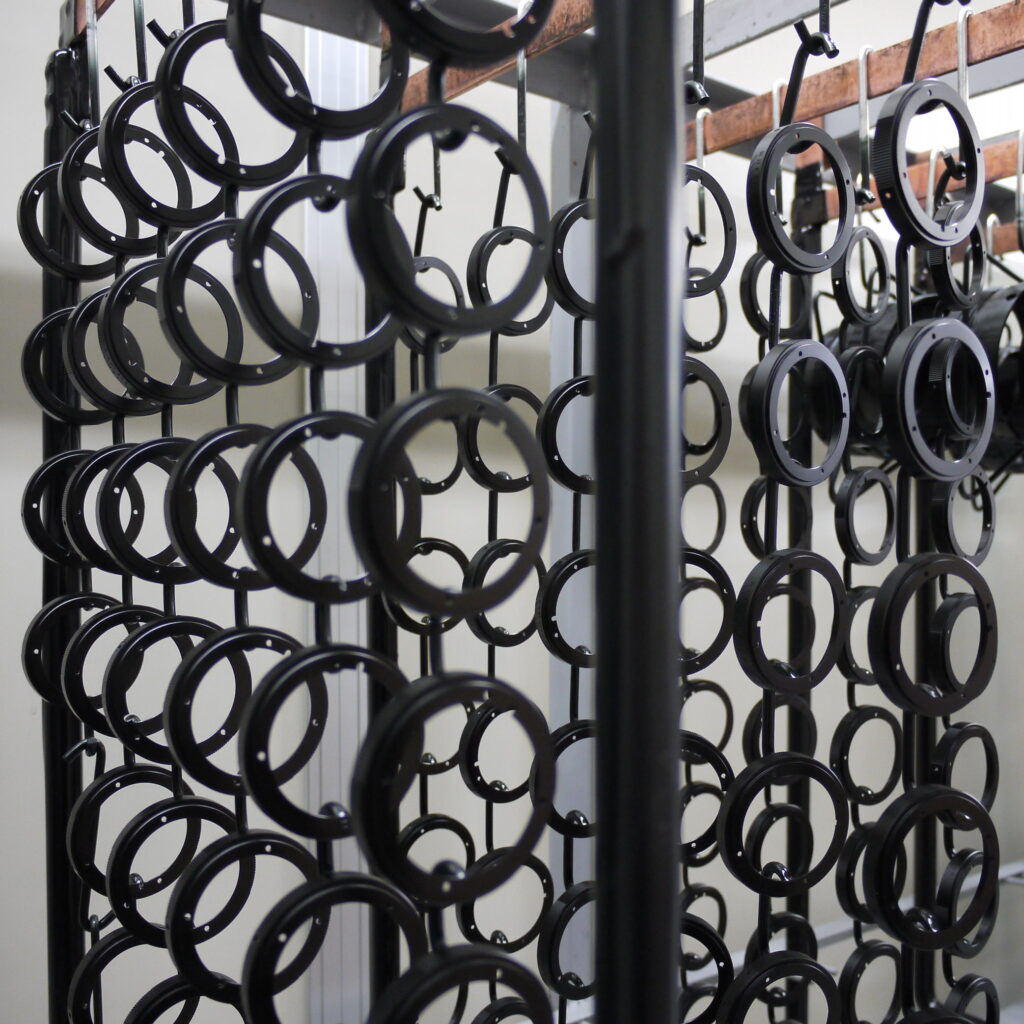
The above photograph shows a batch of rings that have been just black anodized using a large automated unit at Nakano factory. Bare aluminum that has been milled from stock is vulnerable to scratching and the surroundings, so surfaces are treated to improve corrosion resistance and wear resistance, and to dress the metal with coloring. This is known as “aluminum anodizing” or “alumite-processing.” This process forms a tough film on the surface by electrolyzing the aluminum by an anode until it oxidizes.
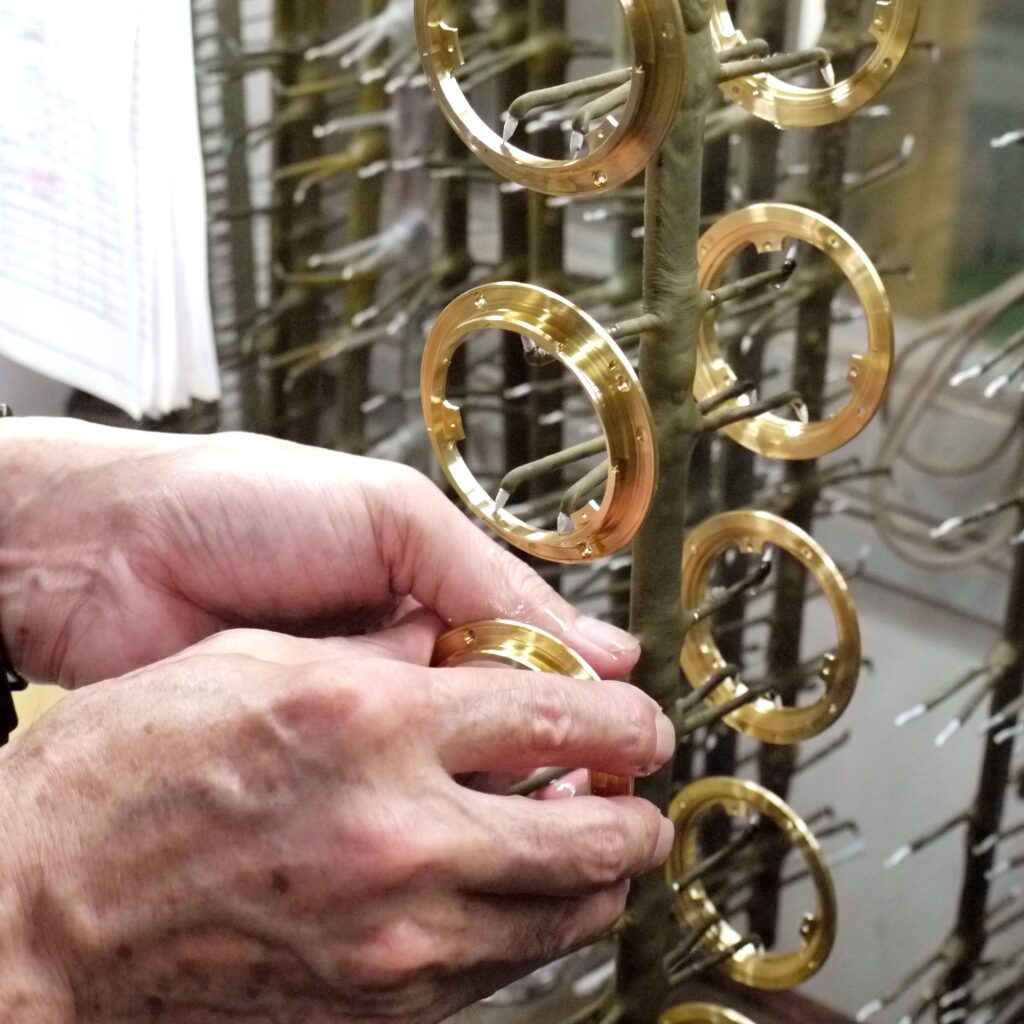
Unlike anodizing, processes for plating parts with nickel, chrome or other material have yet to be automated, so they are done manually. In fact, every chrome-finished component on the exterior of a high-end optical product is processed by hand. Here, the secret to high quality electroplating is to remove any oily films from surfaces so that the plating material tightly adheres. In contrast to this, brass parts are heavily coated in oil when sent to the plating process to keep them from oxidizing because exposed surfaces of milled brass start oxidizing immediately. Therefore, three baths are prepared just for degreasing and thoroughly washing these parts. The cleanliness of these parts is checked with the human eye. In other words, they are visually inspected.
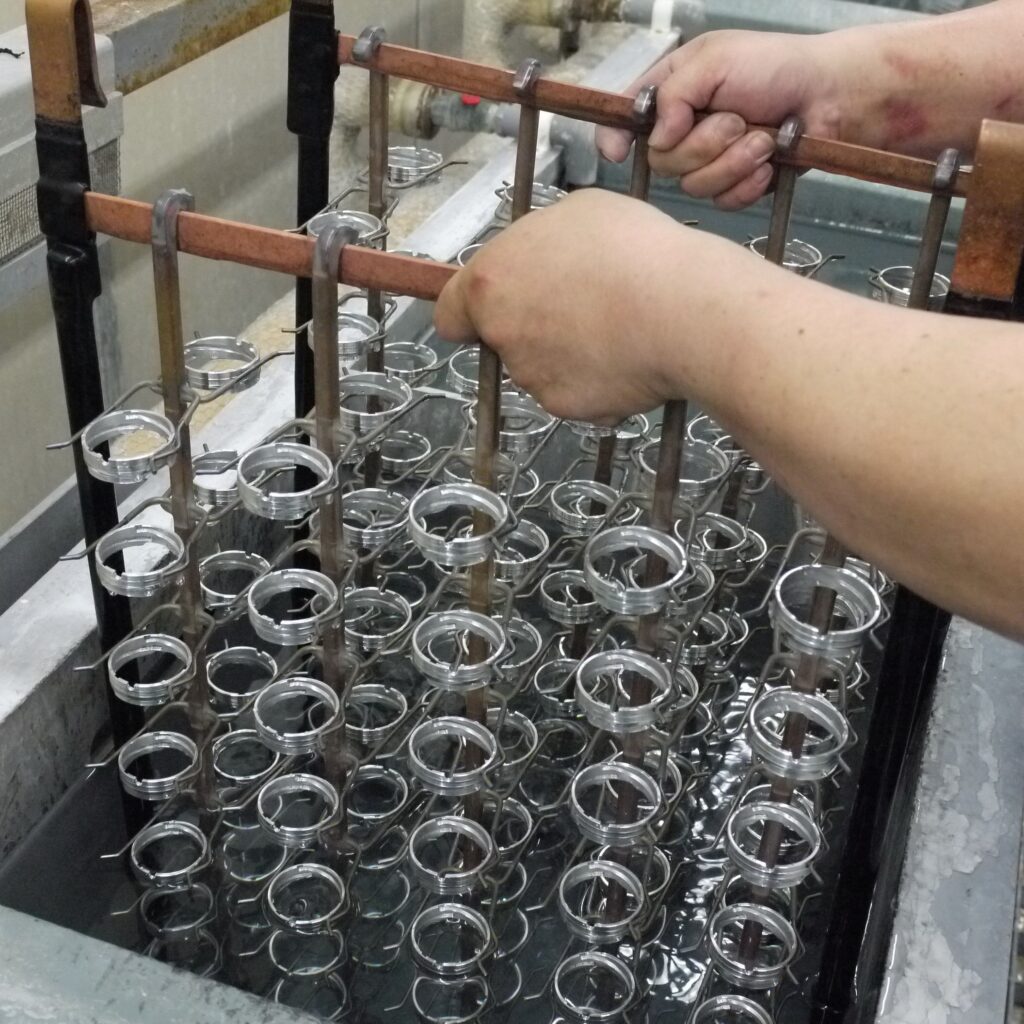
When completely washed, the metal surfaces of these parts are hydrophilic, meaning that a water film clings to them when lifted out of the water bath. This film of water is easily broken by even the smallest amount of hydrophobic contamination such as oil. The film is managed by workers. Washing operations are done under the same kind of sharp eyesight and dexterous handling that dye artisans use to make traditional handicrafts. Of course, it is likely that functional requirements such as surface hardness and corrosion resistance could be obtained via automated processes, but doing this manually still is better as even the slightest variance in tone or thinning in the plating can be detected. A beautiful, shiny and flawless plated finish is one of the quality parameters we insist upon for high-end optical products.