レンズの素性を決める、研削の技
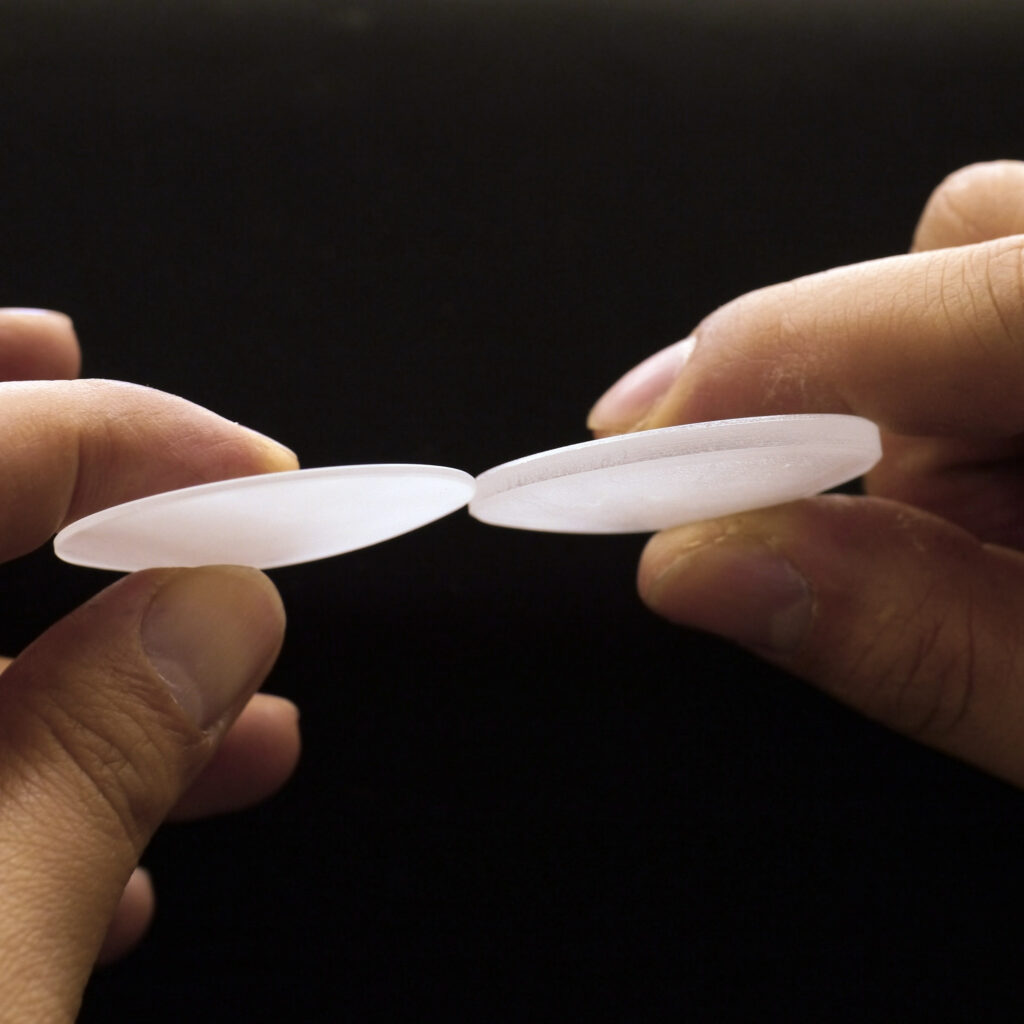
カメラ用交換レンズには、鏡筒内に何枚もレンズが入っています。サイズや凹凸の形状、屈折率などの光学的仕様はそれぞれに異なり、まさに多種多様です。これらのレンズを製造する重要な工程のひとつが研削です。上の写真はプレス加工によっておおまかに形づくられたレンズの原型(右側)と、設計仕様で指定された表面曲率まで研削されたレンズ(左側)の比較です。かなり厚みが違って見えているとおり、ガラスの表面付近に発生する材質の微細なムラを取り除き、内部の良質な部分だけでレンズは作られます。純度を求め素材を削り込むという点では、徹底的に精米して外側の余計な成分を取り除き、“でんぷんだけの白米”で造られる大吟醸酒と同じです。

研削には、カーブジェネレータと呼ばれる装置が用いられます。カップ状のダイヤモンドホイールを、加工物である光学ガラスに斜め方向から当てていきます。このカップとレンズの当たる角度を変えることで、さまざまな曲率(カーブ)を持つレンズを製作することが可能になるのです。凸レンズ、凹レンズともにカーブジェネレータで1枚1枚が加工され、指定された表面曲率に準じた曲面が形成されていくのです。研削された表面は磨りガラスのように白く曇って見えますが、ほとんどこの段階で曲率に関するレンズの精度は決まります。すなわち研削工程がレンズの素性の善し悪しを決定してしまうのです。

レンズの曲率は、対象物の外周と中心部の長さの差異を感知するスフェロゲージで計測します。ゲージの中心部から出ているプローブと、計測するレンズの中心を合致させると規定値からどれだけズレているかが判るのです。ただし、このゲージは設計図どおりの数値にはセッティングされていません。このあとの研磨工程を考慮して、ごく僅かに設計より少ない値にシフトして設定することで、オーバーコレクションを防いでいるのです。光学ガラスを削ることによりレンズに仕上げていく工程では、削り過ぎは許されません。次工程での磨きしろを確保しながら、作業負荷を最小限にするポイントを見極める。この“頃合い”こそ、蓄積された経験と技術なくして判断できないこだわりの技なのです。