Adamant about cutting glass blanks by hand
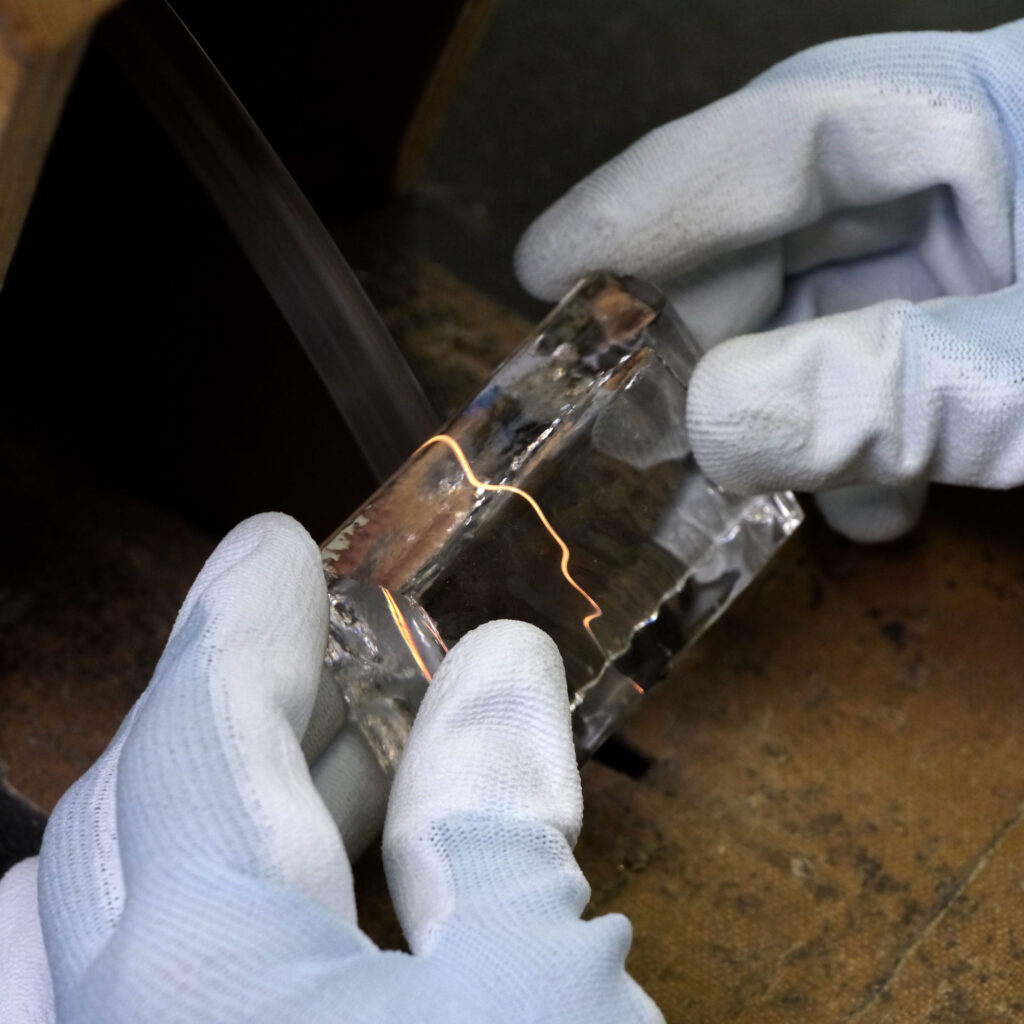
Cosina’s Obuse factory makes lens blanks, and the first step to that is to prepare the necessary quantity of glass material. Too little material is not even worth considering, but too much is wasteful. The required quantity is determined by calculating the diameter and curvature of each single lens to be made from the glass material specified in design specifications of the high-end optical device. The above photograph shows a piece of optical glass that are cut by hand for working into a blank. A blank is made by pressing a bar of optical glass against a metal disk that is rotating at high speed. In just a few seconds or so, the bar is locally heated by friction and splits into two pieces. This technique uses thermal stress to cut fragile materials like glass and, since it generates less scraps than cutting edge faces with a blade, less material is wasted.
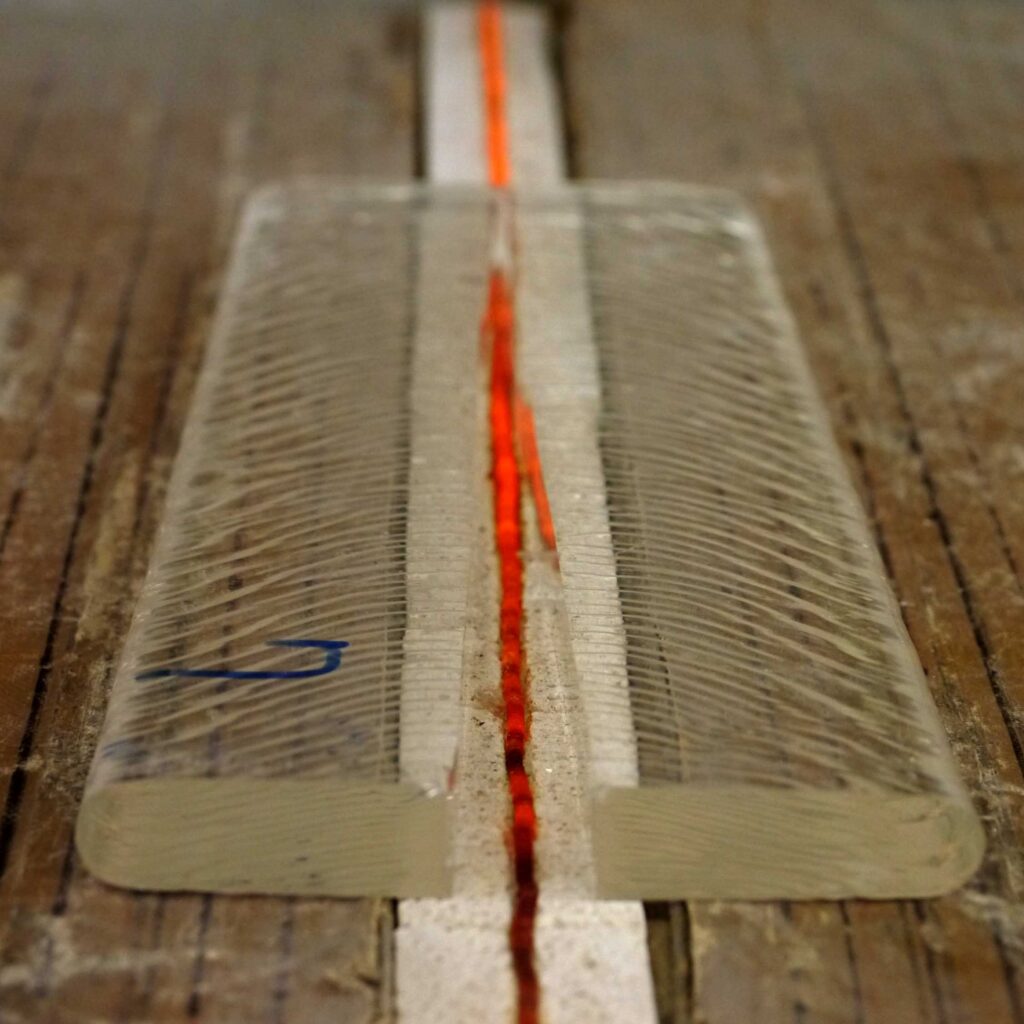
Thermal stressing is also used to cut bars into large pieces, too. This is done by electrically charging a nichrome wire positioned so as to heat the bar along the cut line. The heated part of the bar expands and causes stress in unheated parts. At just the right moment, the cut line is struck with a wedge to split the bar into two. This is yet another job that requires skill, but Cosina has practiced and maintained this technique since the company was founded. Our familiarity with the toils and troubles of optical glass manufacture has made us adamant about not wasting anything and, as a result, helped us to reduce the amount of waste we produce.
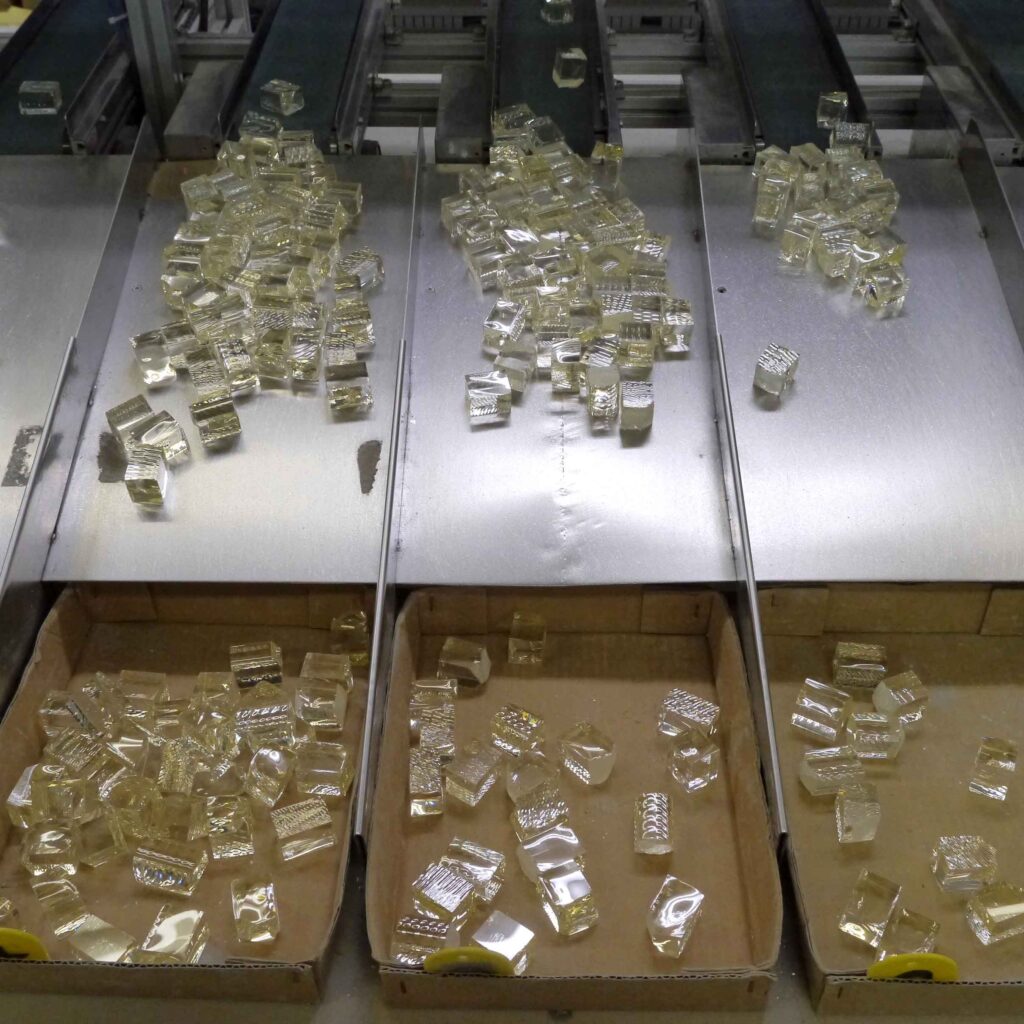
Experience and know-how enable us to cut optical glass blanks to the required weight. The infinitesimal differences in weight are classified into groups by precision weighing, before the blanks are sent to the next process. However, we do not use gravity weighing. Though considered quick and highly efficient by most, gravity weighing runs the risk of scratching or chipping the optical glass. All of our decisions are based on “consideration for optical glass.” By the way, the end pieces and trimmings that unavoidably result in cutting are stocked to make lenses of the same glass material but smaller diameter and thickness, so there is very little that gets thrown away.