Optical elements wrapped in transparent sheets
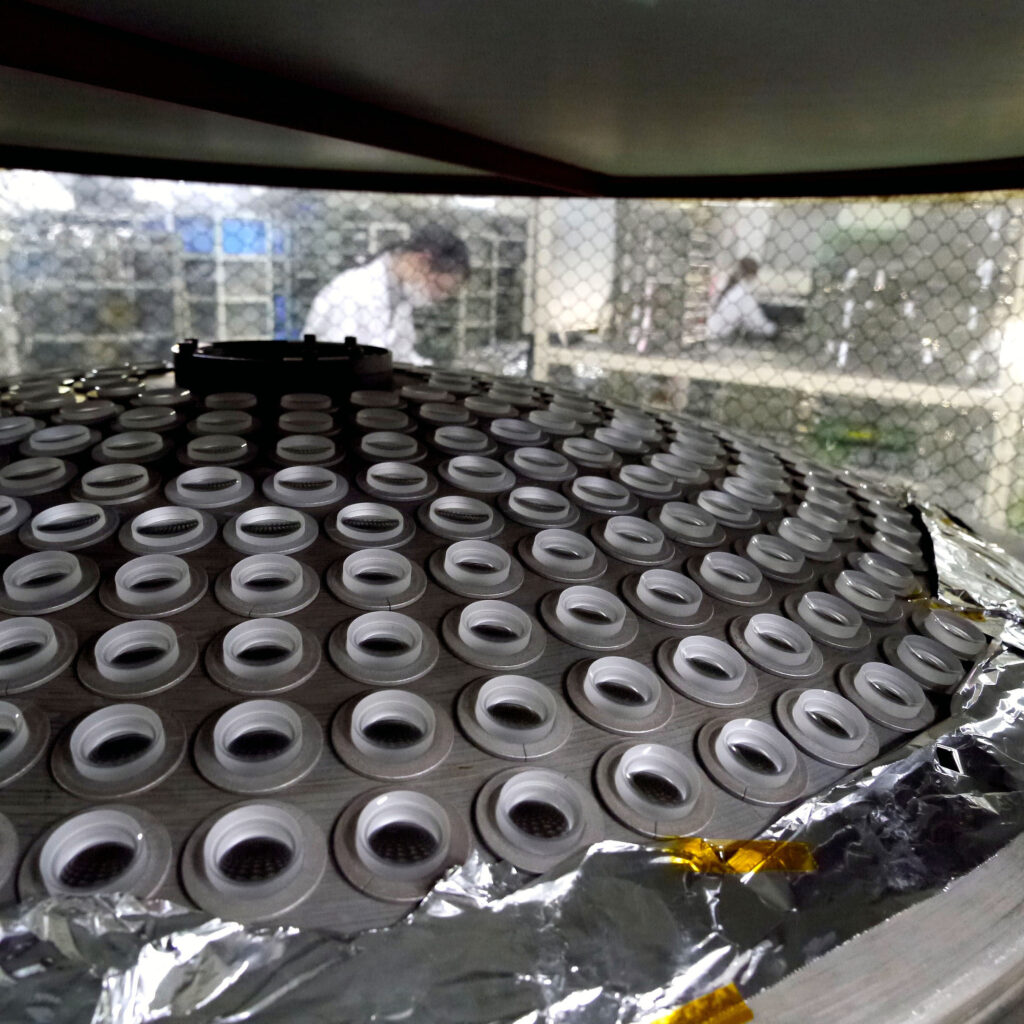
The coating process can be done not just for a single element but multiple optical elements of the same specifications as well. The above photograph shows optical elements ready for coating by vacuum deposition. The operators beyond the batch of optical elements mounted on the dedicated carrier are blurred. This is not due to problems with the camera or lens used to take the photo. It is because the outer boundary of the carrier is surrounded by a highly functional flexible sheet. This sheet prevents adhesion of airborne dirt to the glass surfaces while the optical elements mounted on the cylindrical carriers are waiting for the coating process. Because the photo was taken through the transparent veil, the view of the Nanase factory is blurred.
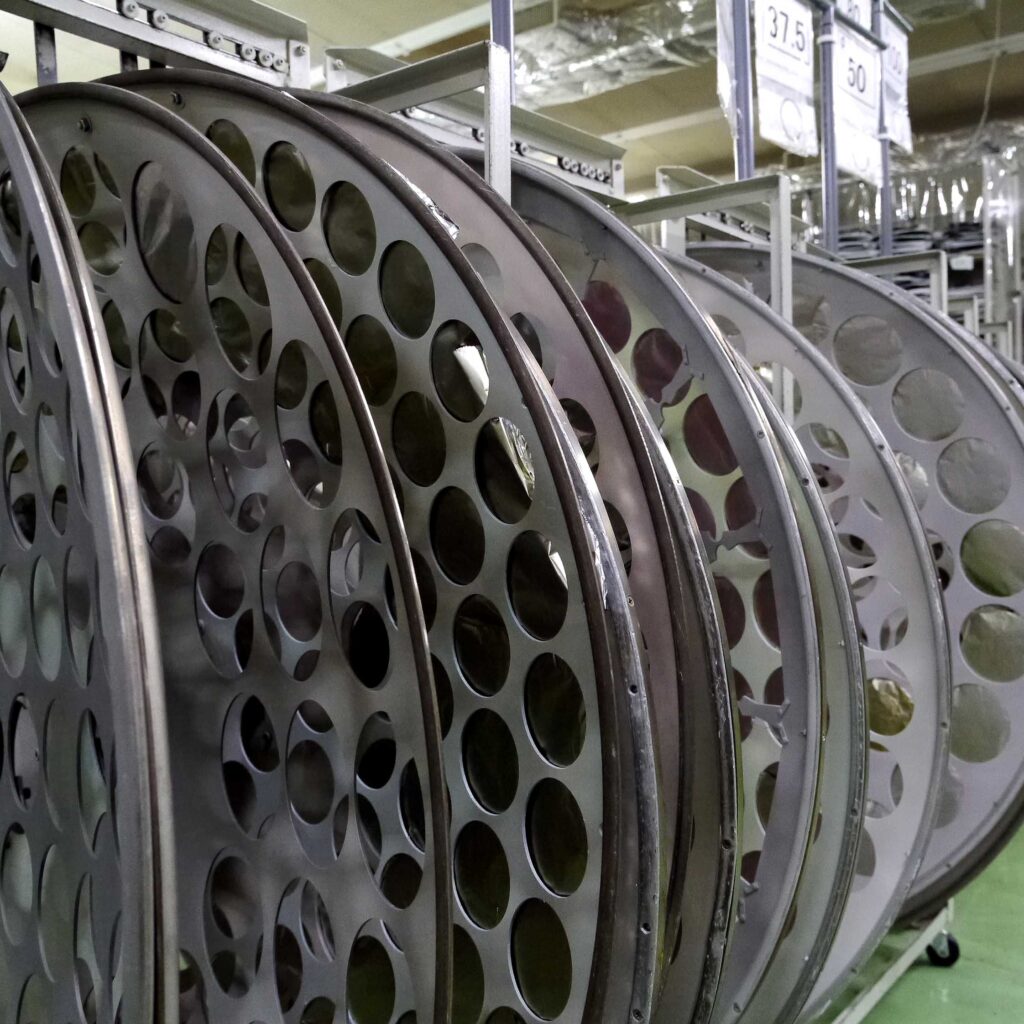
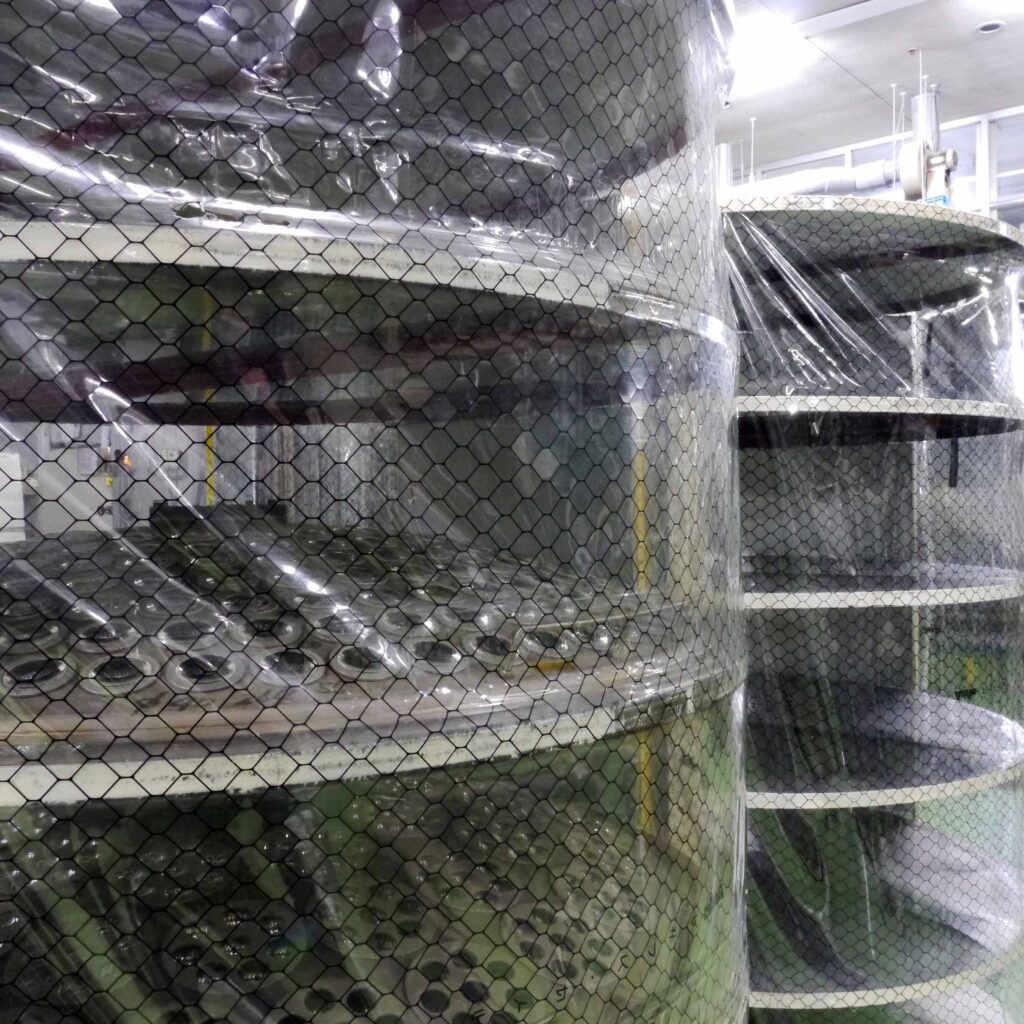
As the preparatory stage for coating, the optical elements are mounted on tables called “coating domes.” These dome-shaped tables are used for forming optical thin films inside a vacuum deposition system. The coating domes are essential for ensuring optical glasses are uniformly coated wherever located on the dome. They bulge like domes to allow the molecules of the coating material that have been vaporized into a gas inside a vacuum, to circulate homogeneously. The conditions change according to the diameter of the optical elements and the curvature of the coating surfaces. So, coating domes are prepared according to specifications.
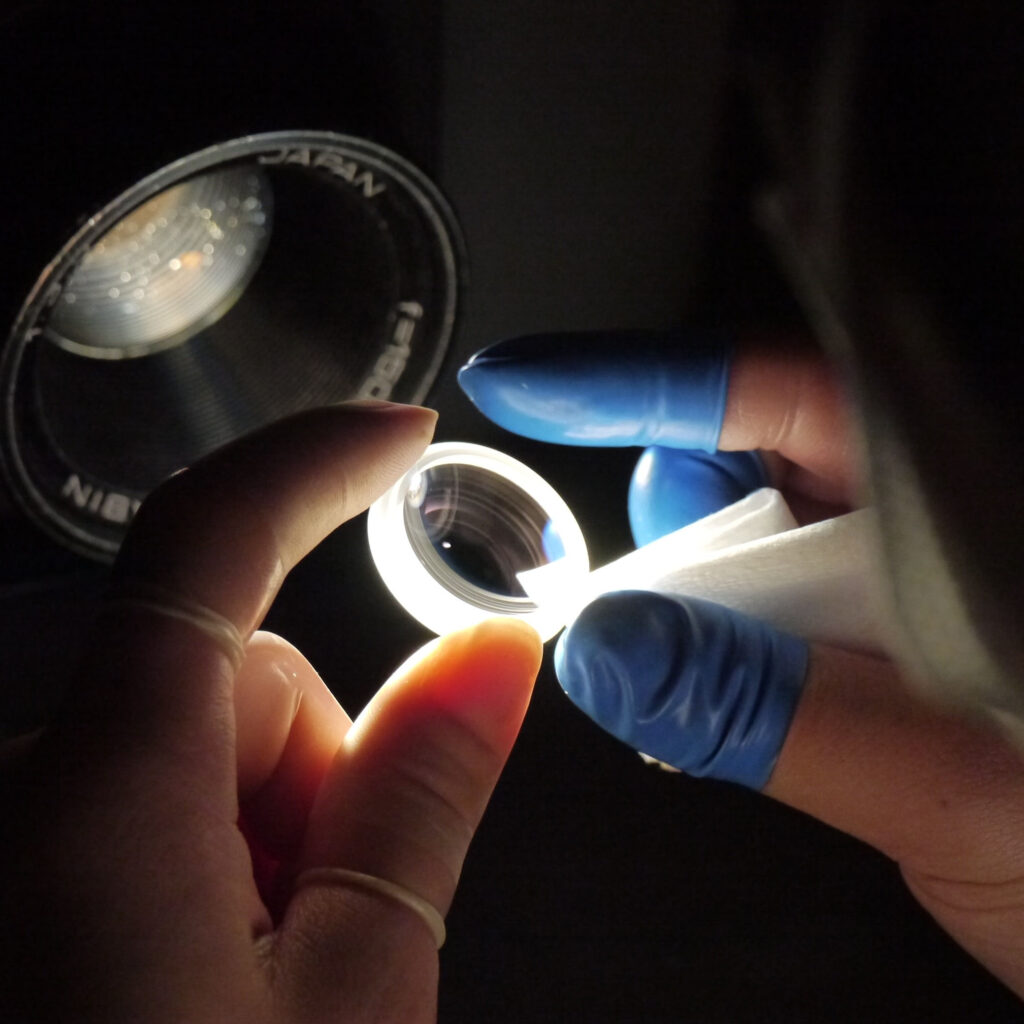
All optial elements that have been polished to the required curvature are manually cleaned just before the coating process and are subjected to visual inspection under light. If even the slightest tarnishing or dimming is detected, the optical element is not sent to the coating process. The optical elements that pass this rigorous inspection wait for vacuum deposition under the protection of transparent sheets shown in the above photograph. Such efforts may make some of you feel we are excessively nervous, but it is essential for maintaining the high quality of our products.