Vol.2:機構設計者
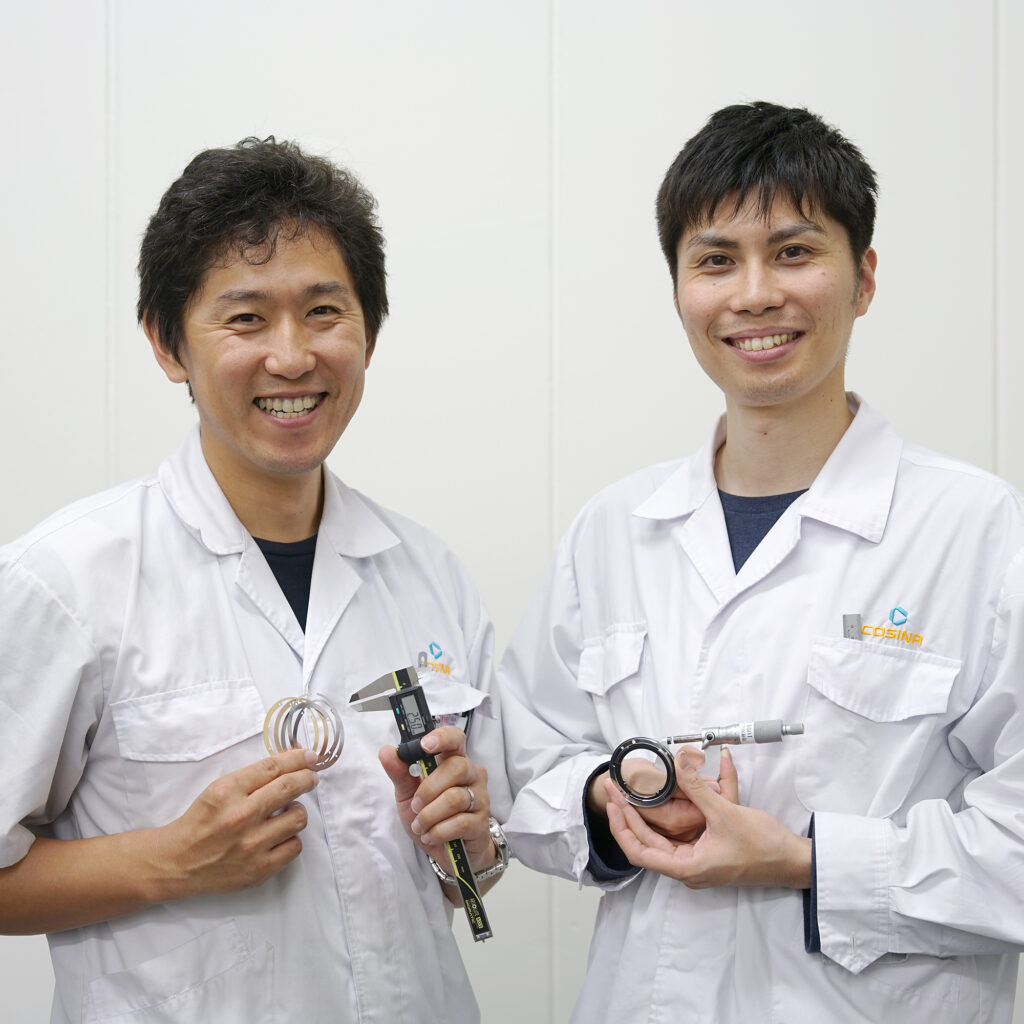
技術・開発課
第一設計グループ 主任
黒岩洋平(左) 滝澤旬平(右)
機構設計のミッションは、光学設計から受け取ったレンズ構成を元に、それが製品として機能するための部品構造を、形状・サイズ・材質・操作性などを考慮しながら作り上げること。黒岩さんは交換レンズの機構設計に長く携わり、BESSAシリーズ10周年記念モデルのNOKTON 50mm F1.1も手がけた経歴を持つ。滝澤さんは今までプロジェクター用レンズを担当。交換レンズの機構設計は今回が初仕事だ。
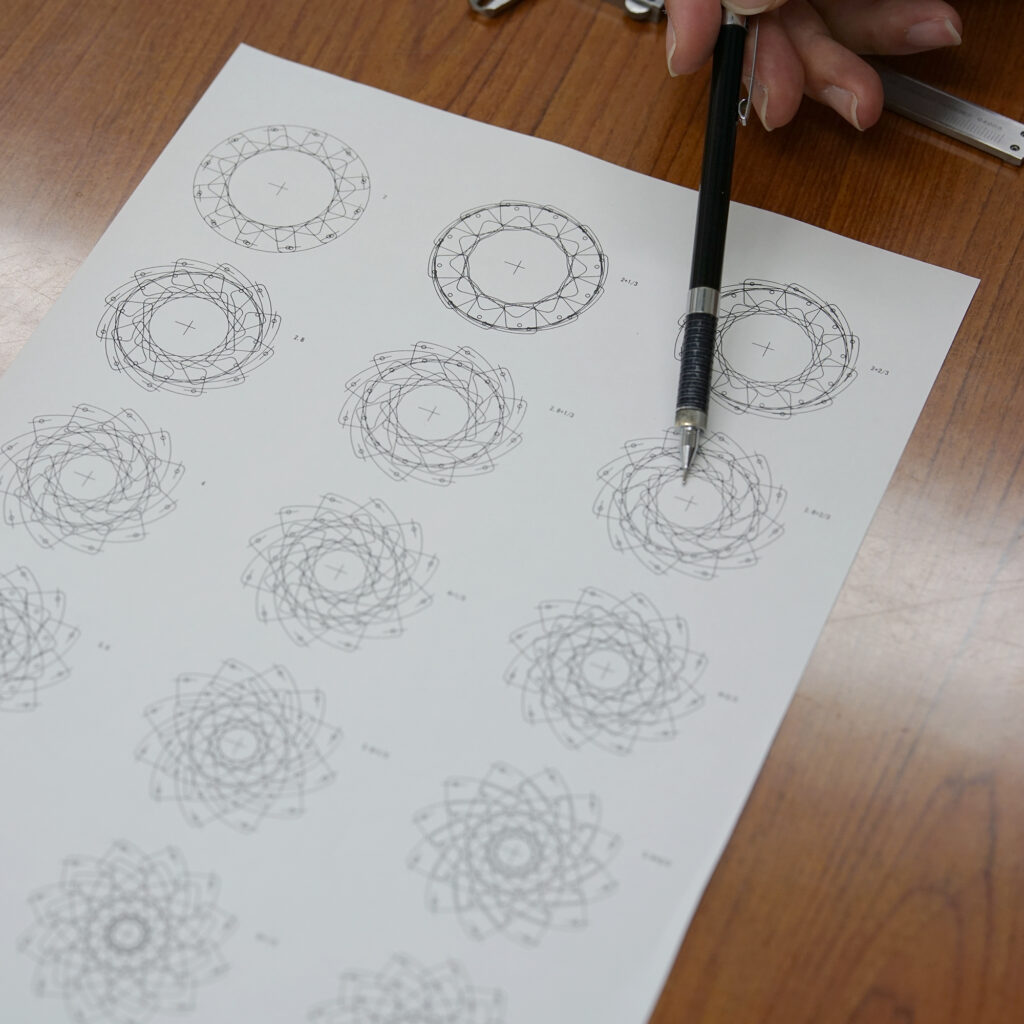
アポランター50mm F2は、開放だけでなくF2.8でも円形になる絞りが採用されています。この絞り羽根を設計されたのは黒岩さんですか?
黒岩「はい。最近では“玉ボケ”を楽しみたいユーザーから円形絞りへの要望が高まっています。レンズは絞り開放では真円になりますが、絞っていくと絞りの枚数が孔の形に影響してきます。昔のレンズで絞りの枚数が非常に多いものは丸に見えますが、実は絞りの枚数角形になっているんです。今回のレンズの場合、12枚の絞りを使っているので12角形になるんですね。そこで絞り羽根の一部を丸くすることで、ある箇所で再び真円にできないかと思いつき、チャレンジしてみました」
開放と最小だけでなく、その途中でも真円になる絞りというのは他に例がないと思うのですが、アイデアを形にするのに苦労されたのでは?
黒岩「通常の絞り羽根は、ある程度数式化できて面積の計算ができますが、これは絞り羽根が作り出す孔の形状がどんどん変わってしまうので本当に一つひとつ手探りでした。ストレートの部分とRの部分が各12個あるので、回転角度に応じてストレートとRの部分がどのように出てくるのかをコンマ1ミリ単位で動かして面積を計算しました。手間がかかるんですけどやらないと実現できないし、やりだしたので最後まで突っ走りました(笑)。結果的に形になってよかったです。いいか悪いかの判断は、お客様からのフィードバック待ちの状態ですね」
今回の設計で、滝澤さんの手がけた部分はどこでしょう?
滝澤「私は基本的な構成を、外観含め担当しました。当初から目標とするサイズ、全長と径がほぼ決まっていたので、あまり大きくできないという制約をふまえて外観をどうするかという話を進めていきました。自分の出した試作前の図面を見ると、ちょっと変な外観ですね(笑)。実は交換レンズの設計をし始めたのが去年からで、それまで私は別のグループでプロジェクター関連の設計をしていたんです。交換レンズを手がけたのはこれが初めてで、どんな外観がいいんだろう? と考えることから始めて、最初は絞りクリック・デクリックを切り替える構造を搭載する予定がなかったのですが、せっかくコシナ創業60周年記念モデルなので入らないかと」
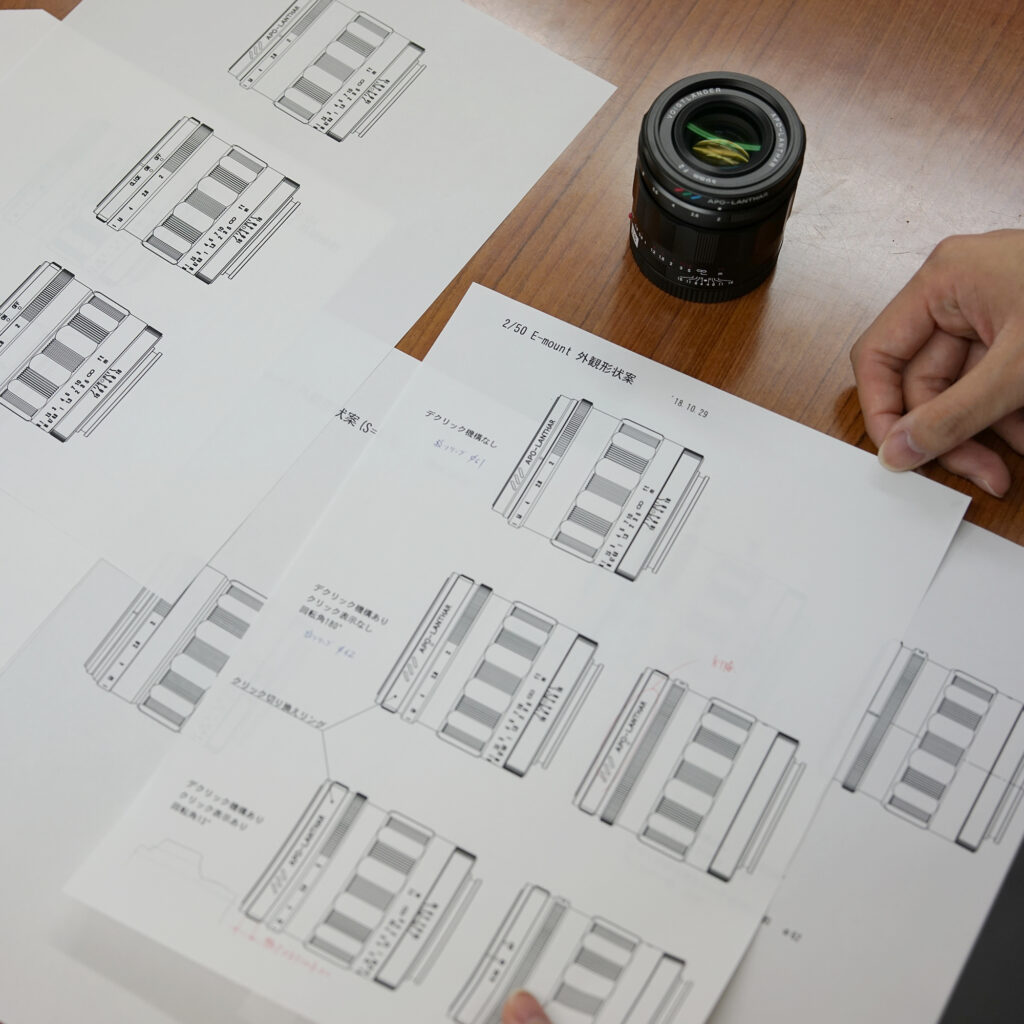
サイズの制約があるのに機構部品を追加していくというのは、黒岩さんの絞り羽根と同様に難しい仕事だと思います。この課題を突破していくために、何かアイデアが盛り込まれていますか?
滝澤「結果的に基本構造としてはマイクロフォーサーズと同じタイプを採用したのですが、そのままでは目標とするサイズに収まりません。フィルター径もφ52になってしまうので、使い勝手は今まで通りで省スペースに収めるのに苦労しました。Eマウントなのでエンコーダ系があり、フローティング機構も採用しているので動きが複雑になる中、かなり狭い空間で各機構の取り回しをやりくりして設計を進め、最終的にフィルター径をφ49に持っていきました。今まで板バネを使っていたのをコイルバネに変えることで小型化できました。板バネ自体の部品は薄いですがネジで止めなければならず、ネジの頭の幅と長さが必要で意外とスペースを取るんですよ」
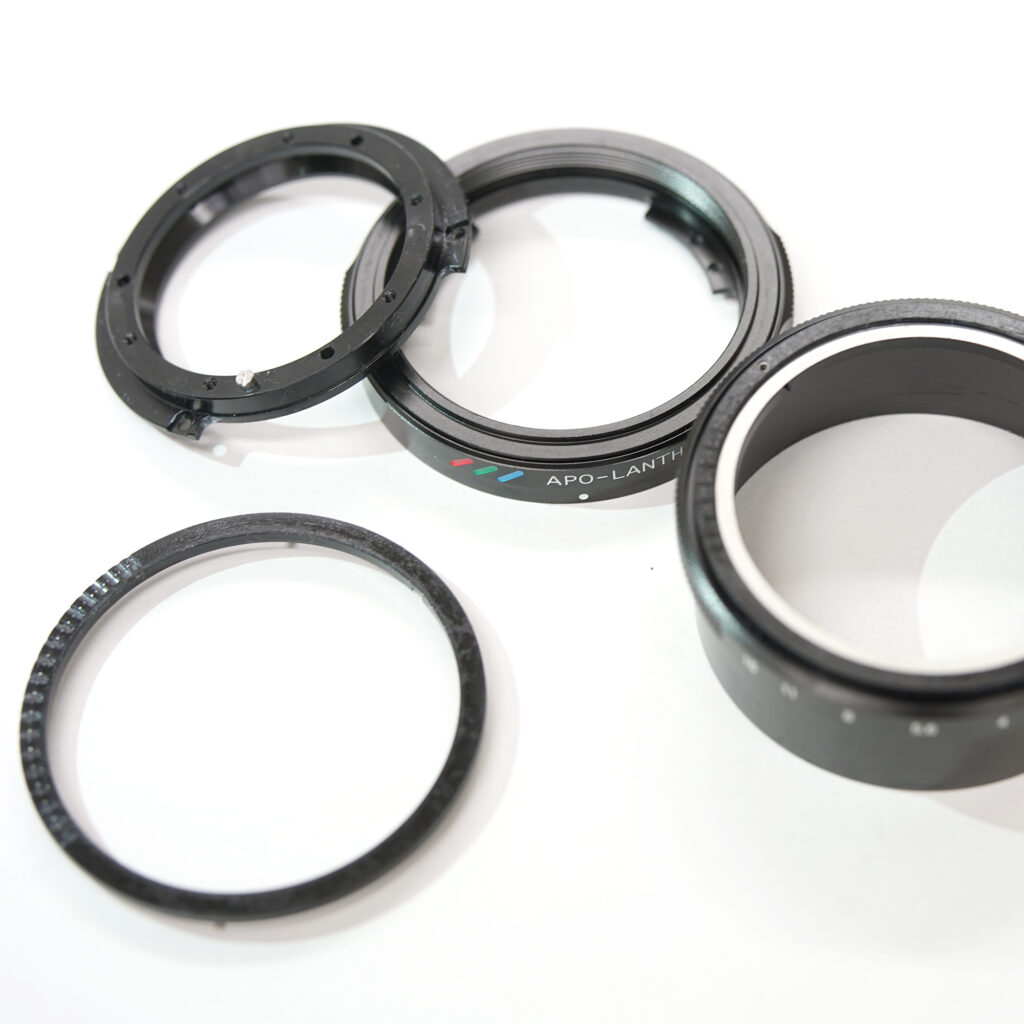
コシナがフォクトレンダーブランドの交換レンズを設計・製造し始めて20年が経過しました。過去の製品と比べて変化している部分はありますか?
黒岩「光学的な精度を上げるために、調整機構が増えています。1999年に発売していたレンズでは絞りの前後を2分割して、枠2つでレンズを保持していました。今は絞りの前側で2つ3つの枠を組み合わせて作り、絞りの後ろにも2つ3つの枠があって、それぞれレンズの間隔と軸の調整をして組んでいきます。ただ枠をねじ込むのでなく調整するにはビスが必要になるのですが、ビスの頭のサイズが大きいとかスペースをとるとか、少しの違いの積み重ねで外径への影響が出てくるのが最近の設計の難しいところですね。コンパクトに仕上げながら、組み立ての段階で調整しやすい機構を考えて作ることも重要です」

逆に、変わらず心がけているポイントはありますか?
黒岩「これはユーザーさんが写真を撮る場面ではないですけれど、修理する際にリワークしやすい機構であること。例えば外装パーツは光学系にまで影響を与えずに分解できる構造にしています。外装が傷ついてしまって交換する場合に、時間をかけずに交換できることは頭に置いていますね。あとは無理のない、理にかなった構造である事ですね。毎年CP+では製品のカットモデルを展示します。あれで機構は丸裸にされていますから」
滝澤「中身を見たい方はCP+の展示で(笑)。大量生産が前提のメーカーであれば分解修理するよりも廃棄して、新しいモジュールと入れ替えた方がコスト的には有利なのでしょうけれど、フォクトレンダーは数が少ないぶん直せるものは直していけることが設計の基本方針です。正直なところビスで止めるよりも部品を接着した方がスペースを稼げますが、やはり信頼性や長い期間お客様に使っていただくことを考えると、なかなかそこには行き着かないかなぁと思います」
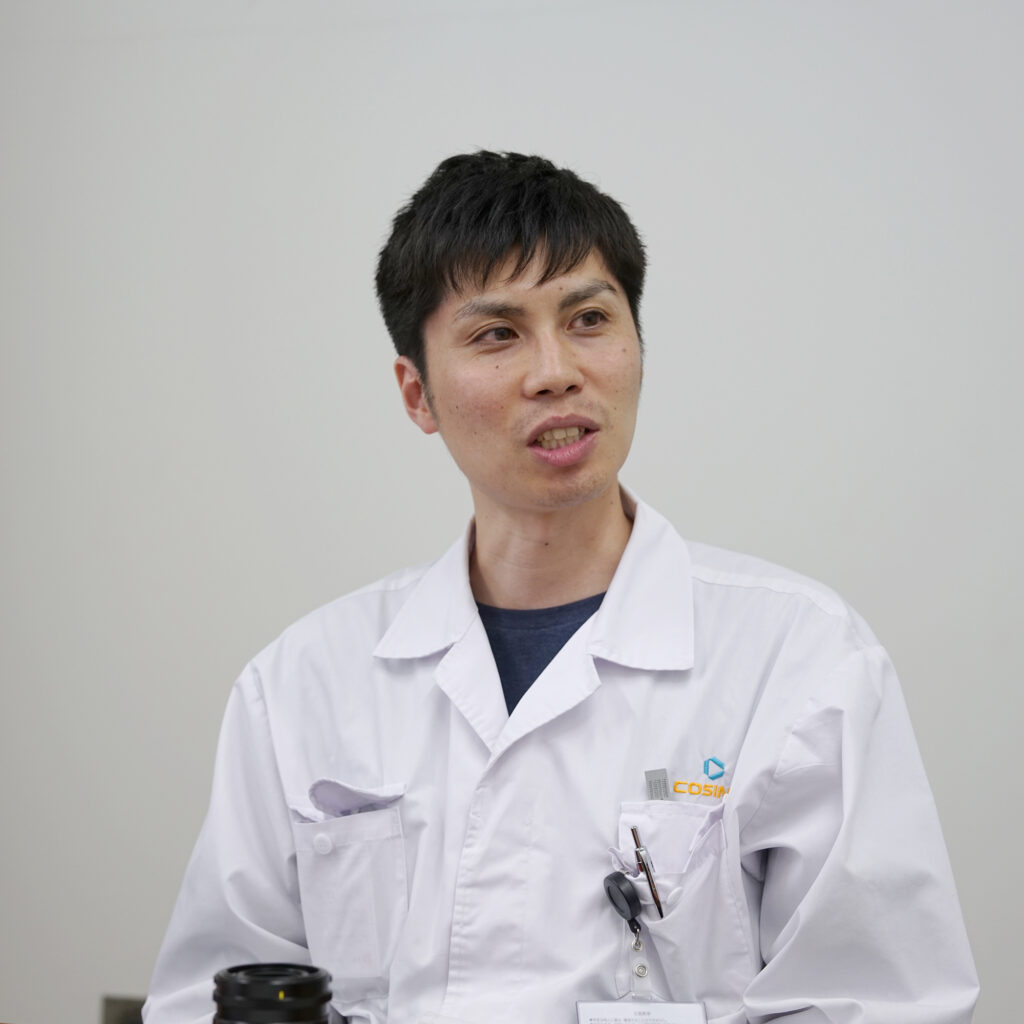
他メーカーの製造する交換レンズの中を見て、やはり違いを感じますか?
滝澤「プラスチックであれば調整用の部品にちょっとスロープをつければレンズ間隔を変えられる構造になりますが、切削した金属ではそれができません。垂直は垂直、水平は水平のポイントが決まっているから、内心『これプラスチックにした方が効率いいかも』と思うこともありますが金属は精度が高くメンテナンスやリワークに優れていますので。」
黒岩「だから、正直『ここがプラスチック?』とか思うときはありますね。でも、プラで作っているメーカーの人たちが私たちの設計しているレンズを見たら『こことここの機能を、プラ部品で一緒にしちゃえばいいのに』と思うかもしれないです(笑)」